Industrial water chillers are utilized to attain the best temperatures in various manufacturing operations, data centers, and industrial applications. Among all the models of chillers, the Water-Cooled Industrial Water Chiller is the most effective and efficient model. In this article, the working principle of Water-Cooled Industrial Water Chiller Equipment is discussed thoroughly, along with its parts, functionality, and advantages.
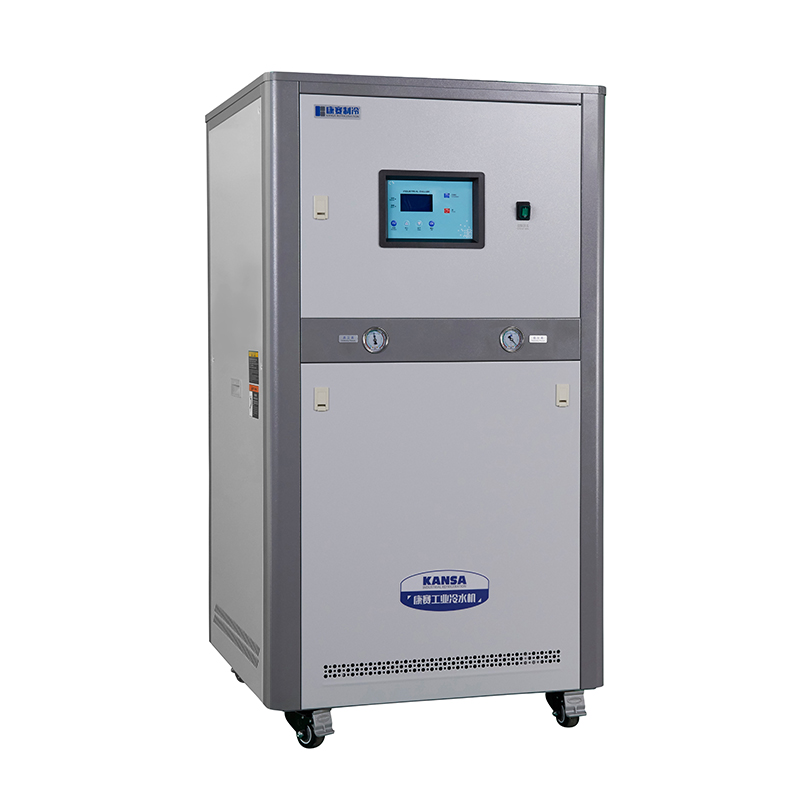
Main Parts of a Water-Cooled Industrial Water Chiller
A water-cooled industrial Water Chiller has several key parts that take part in industrial process heat extraction:
- Compressor – The chiller’s main component, where the refrigerant is compressed and sent to increase its pressure and temperature.
- Condenser – Transfers heat from the refrigerant through cooling water, converting it from high-pressure gas to liquid.
- Expansion Valve – Regulates the flow of refrigerant to the evaporator, reducing its pressure and temperature.
- Evaporator – Removes heat from the process water, cooling it prior to return to the industrial process.
- Cooling Tower – A support system that dehumidifies the condenser water through evaporation prior to its return to the chiller.
Working Principle of a Water-Cooled Industrial Water Chiller
Water-Cooled Industrial Water Chiller Equipment adheres to the vapor-compression refrigeration cycle in four stages:
1. Compression
Low-temperature, low-pressure gas is pumped in as the refrigerant. Its pressure and temperature are increased, and it’s converted to high-pressure, high-temperature gas by the compressor.
2. Condensation
Hot refrigerant gas is sent into the condenser and is cooled by the application of cooling tower water. During the process of passing the heat to the cooling water, the refrigerant is converted to high-pressure liquid.
3. Expansion
High-pressure liquid refrigerant goes through the expansion valve and, in the process, undergoes its pressure as well as temperature both drastically decrease. It sets it up for the process of heat absorption at the evaporator.
4. Evaporation
Cold refrigerant is pressurized into the evaporator, where it absorbs process water heat from the industrial process. In vaporization, the refrigerant is converted to a low-pressure gas, and chilled water is re-circulated to the application.
The cycle is continuous to deliver the required cooling in industrial applications.
Advantages of Water-Cooled Industrial Water Chillers
Unlike air-cooled systems, Water-Cooled Industrial Water Chiller Equipment has several advantages:
- Increased Efficiency – Water is a more efficient heat transfer fluid than air and can provide improved cooling.
- Lower Operating Costs – Water-cooled systems consume less energy, especially in heavy industry use.
- Lower Noise – Since the condenser is water-cooled rather than fans, noise is significantly reduced.
- Increased Life – Lower equipment thermal stress translates to increased equipment life.
Applications of Water-Cooled Industrial Water Chillers
As its superior cooling capacity, Water-Cooled Industrial Water Chillers are used for multiple functions within:
- Plastic Injection Molding – Prevents overheating in production.
- Food & Beverage Processing – Offers accurate temperatures for quality assurance.
- Pharmaceutical Production – Offers consistent conditions for high-risk applications.
- HVAC Systems – Used to allow commercial building-sized air conditioning.
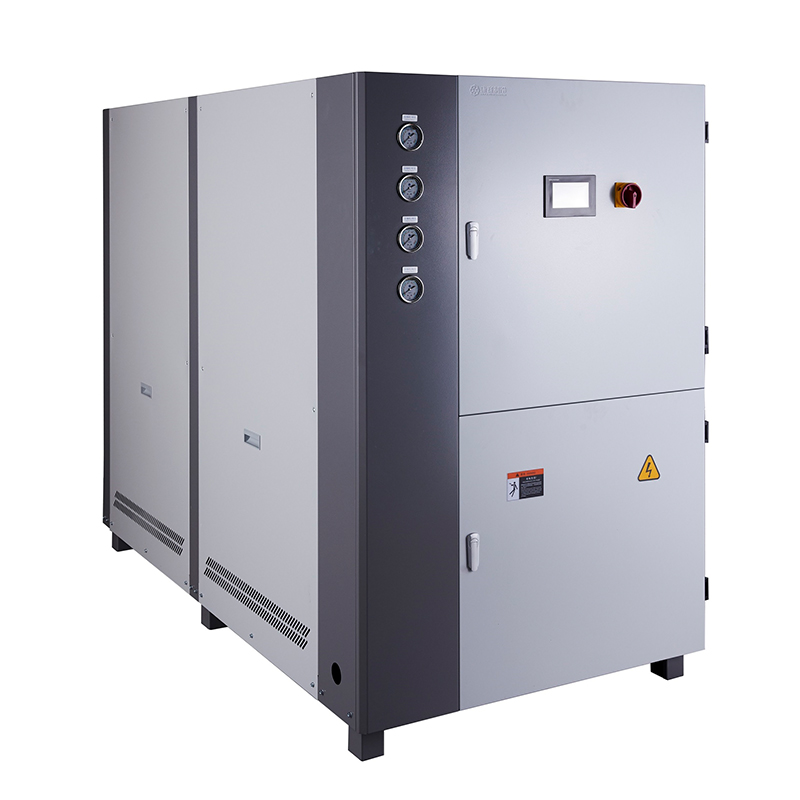
Conclusion
Water-Cooled Industrial Water Chiller is the best industrial process cooling system. With water as the coolant, this Water-Cooled Industrial Water Chiller Equipment gives optimum performance, energy savings, and durability. Having knowledge of its working principle allows industries to select the proper chiller system for their specific cooling requirement.
No matter their use in manufacturing, HVAC, or process cooling, Water-Cooled Industrial Water Chillers remain an important component of operational efficiency in most industries.